There's a picture going around now of a dress. And there's a surprisingly firm split in how people perceive it. Some say the dress is "obviously" white and gold, others say it is "obviously" blue and black.
I think, like the airplane-on-a-treadmill one, the problem lies not with esoterics of color perception, but in definitions. Do you mean the colors that are in the picture, or the color the real object is likely to be?
The latter is, of course, not possible of derivation from the image supplied. It is obviously taken in strong backlight, the lighting and tones are strongly suggestive of outdoors in sunlight on a clear day, and the trim appears at the least of a satin finish, possibly even shinier.
But you don't know the response curve of the CCD or what adjustments the image has been through. So, based on what evidence is available, the conservative hypothesis is white or off-white with a trim that is somewhere between gold, metallic copper, down to a light coppery-brown with a slight sheen to it.
But that doesn't mean that "is" the color of the dress. Like so many things, it depends on image steps and local effects (the gamma and color balance of the computer screen you are viewing on, the lighting environment you are sitting in while viewing it, etc.) Given these, a wide range of individual colors is possible. Up to and including black trim if you define "black" as a satin finish with a surprising amount of yellow sneaking in.
It's like the problem of the color of the Martian sky. To what color perception? Your eyes naturally gray-card in every environment they are in (up to a certain range; they can't compensate all the way down to candle light, and strongly saturated color environments -- like viewing the world through rose-colored glasses -- will retain a tint even after an hour of adjustment.) If you were transported instantly to Mars, you might see the sky as one color. If you were standing out there all day, adjusted to the sunlight there, you'd see another.
And it is absurd that people who work every day on computers, people who often are involved in art and image as part of their jobs, don't even see the need to point this out when discussing the dress.
This underlies one again this lacunae that much of my profession hits over and over again. When I do lighting or sound I have no choice but to grapple with what is actually there. And to do my best to shape the audience perception in the directions I want.
The vast majority of the people I work for and around can only work on the level of what they perceive, and conversation stops dead on that bottleneck. Because I am well aware it looks dark or sounds soft, and I am taking steps to ameliorate this, but those steps have little or nothing to do with turning up the lights or the microphone feeds.
Tricks of the trade, discussion of design principles, and musings and rants about theater from a working theater technician/designer.
Friday, February 27, 2015
Wednesday, February 25, 2015
Knot Working
I still need another job.
The props stuff is keeping me busy, but with only a sound op gig, a small lighting design, and some microphone rentals I'm just barely going to scrape by.
I was messing around with knotwork today -- or more specifically, looking at a lot of stuff about Islamic interlace patterns. The idea was to work up something for my new Jedi Holocron project that takes the "Millennium Falcon Circuitry" pattern of the last one and moves it to more of a repeating decorative pattern...and the religious-art connotations don't hurt, as this is a design for a Jedi Temple.
Not sure why I thought of going in that direction. Maybe memories of the fantastic clockwork facade of the Institut du Monde Arabe in Paris.
The props stuff is keeping me busy, but with only a sound op gig, a small lighting design, and some microphone rentals I'm just barely going to scrape by.
I was messing around with knotwork today -- or more specifically, looking at a lot of stuff about Islamic interlace patterns. The idea was to work up something for my new Jedi Holocron project that takes the "Millennium Falcon Circuitry" pattern of the last one and moves it to more of a repeating decorative pattern...and the religious-art connotations don't hurt, as this is a design for a Jedi Temple.
Not sure why I thought of going in that direction. Maybe memories of the fantastic clockwork facade of the Institut du Monde Arabe in Paris.
So I'm slowly getting used to both Inkscape, and GIMP. Flipping back and forth between them is still...interesting...however, as the key commands are completely different for each. In fact, because Inkscape is running on Xquartz via a Java VM, it remaps command (Mac standard) to control. So something as simple as saving the file takes an extra little bit of concentration.
I still have no idea how to proceed on my power issues with the DuckLight. Seems like I need to live with the idea of larger battery packs if I want the full output power, and add on-board regulators. Which not only adds parts, and footprint, but also means you'd have to change jumpers or something for all those applications where a smaller battery pack is more appropriate.
Hrm. Maybe regulating the ATtiny down to 3.3 volts regardless of battery source makes the most sense. 2xAAA just doesn't light anything but a red LED anyhow, and that's the only set that would be too low for even an LDO. And with a powerful enough regulator, it could supply an XBee, meaning I wouldn't really need a custom daughterboard for those.
One thing I have figured out is what I want to do with those flexible USB lights I picked up for a buck each at Wallgreens. Make little Steampunk-Tiffany task lights out of them. Add a laser-cut acrylic clip/magnet on one end, paint the flexible rod up a nice brass, stick a super blue LED in, and pull some painted/dyed PETG over a hand-carved buck to make a shade.
Now if only I had some sketches I liked for the Raygun. I need to start getting client approval and move into the next design phase!
Monday, February 23, 2015
Jaffa, Cree!
Oh, did I make that joke already?
Internet is back, BTW. It took eight phone calls, an hour of navigating phone "help" menus, three service calls, and over a week...but they finally figured out the modem was dead. You'd think they could ping it and find out, but apparently that particularly modem typically fails in a way that looks like a bad line from both ends. Funny thing is, not even the service techs...two of them, lugging bags of electronic gear from their van...had tools to see if the line actually connected. Only a DSL modem will actually tell you anything, and because of the secure installation procedure it is non-trivial to swap in a test unit.
Only good side to the affair is it gave me the excuse to yank my old desktop and monitor and all the associated cruft and clean up under my work table. It looks much neater and cleaner now, and I can use my scanner without getting a back injury.
Discovered a puzzling problem with the DuckLight board. I noticed it was much brighter running off the 5v regulated supply of a USB port than it was off the 3xAAA battery pack. I thought this might be an amperage issue but a little more experimentation shows it to be voltage related.
Which is odd. The forward voltage of green LEDs is under 4 volts (3.7 seems typical). The voltage drop of the AMC7135 chip is a mere 0.12 volts. A 3x battery pack should thus be quite sufficient.
Oh, but wait. Calculating with the smaller voltage of nickel-metal hydride (the Sanyo Eneloop rechargeables I use almost exclusively) brings the 3x battery pack to a mere 3.6 volts. Which is far enough into the curve to experience a significant loss of luminosity.
And I had already discovered that on 2xAAA (my designed footprint for the first board) only the red LED lit properly; the green was obviously not getting sufficient voltage.
Well, shucks. The rated output on lithium polymer packs is 3.3 to 3.7 volts -- meaning once again that the most common green LED chemistry won't light at full power. Especially not if I try to run a 3.3 volt bus (to allow direct connection of certain sensors and XBee radios).
So what are the options? Switching to alkaline is not actually a help. Alkalines drop very rapidly in voltage from full charge. In addition, their nominal rating is given in no-load -- unlike NiMH's, which give the nominal voltage rating under design load (due basically to lower internal resistance).
Going significantly over and regulating down to 5 volts would make sense for a more complex project. At a draw of 1 watt or more, though, that's a hefty regulator -- and a lot of heat from wasted wattage. A dual NiMH pack, for instance, regulated to 5 volts, would have to burn off over five WATTS. That's at the peak of what a TO-220 package can handle with a bolt-on external heat sink.
Splitting the difference, a 4x battery pack delivers 4.8 volts nominal -- that's pushing up to 1/4 of the wattage into the regulator, which has to burn it off -- and at full charge can get pretty close to 6 volts. Which fortunately is while out of spec still within the range of what the ATtiny can tolerate! It is also twice the footprint of the board in flat pack and basically annoys me as a form factor even in quad.
(And in case you are wondering, all those Cree flashlights get away with it because "white" LEDs have a lower voltage drop than the common green ones.)
And, bah -- four fully charged eneloops are sufficiently above the voltage spec that the ATtiny shuts down. Which means I would need to include an LDO in order to operate the green LED at full efficiency. Or....regulate just the ATtiny, perhaps at 3.3V for sensor and XBee compatibility...well, according to the literature the AMC7135 really likes to be between 4.5v and 6v. Gets way too hot above that. Like most LDOs, the highest efficiency is when the voltage in is very close to the voltage out.
Well, I still have to finish porting my "blink" code to the new board, and see if there is even possibly enough space left over in program memory to do any of the other tricks I want. One issue from the old Piranha board that the Cree makes a lot more of a problem is the stair-stepping at the low end of the intensity scale. With only 255 steps in my pulse generator, the difference between 1/255 and 2/255 is a little too obvious in LED intensity. So I'm reading up on dithering techniques. (I can't simply increase the PWM bit depth, as I'm running at 8 MHz on internal oscillator and the PWM frequency is already close to critically low).
I also need to do a bake test to make sure the system can handle being ran wide open for a significant interval. I've already noted that 3W is at the low end of theatrical viability. Fortunately, a lot of applications can be served without full RBG -- instead hanging a 3W or even 10W single-color LED on the board and running the current regulators in parallel mode.
Another change that's on the horizon. The old RGBs are slipping in the Chinese suppliers to make room for new cheaper RGBW's. So far no affordable RGBA, but I have my eye on a few affordable RGB-Warm White already. Which is why my board is a four-channel. And why the ATtiny84 -- to give enough extra I/O pins for external sensors/controls. Although I still may end up just going into an ATmega eventually. Especially if I chose one with native USB support. Those are nasty little surface-mount jobbies...but at least they aren't BGA!
I'm also seriously contemplating revamping my headers completely and making the duckNode Trinket compatible. There's a LiPo backpack in that format, for instance. And in the obverse, I could make my XBee shield cross-compatible. The downside is I want to achieve everything possible from the ICSP header alone -- plus a stand-off, which the current iteration omits -- so there is no need to solder header pins to the board in order to program it or even to integrate it with radio link or power regulation. Having pins soldered on is one more thing to work around or to have to remove when cramming the final board into a prop, and the whole purpose of this exercise is to produce the most minimal footprint, lowest parts count and cost to bring full PWM control of 4W RGB/RGBW LEDs.
(So many TLAs there, I'm starting to feel like I work at NASA!)
Internet is back, BTW. It took eight phone calls, an hour of navigating phone "help" menus, three service calls, and over a week...but they finally figured out the modem was dead. You'd think they could ping it and find out, but apparently that particularly modem typically fails in a way that looks like a bad line from both ends. Funny thing is, not even the service techs...two of them, lugging bags of electronic gear from their van...had tools to see if the line actually connected. Only a DSL modem will actually tell you anything, and because of the secure installation procedure it is non-trivial to swap in a test unit.
Only good side to the affair is it gave me the excuse to yank my old desktop and monitor and all the associated cruft and clean up under my work table. It looks much neater and cleaner now, and I can use my scanner without getting a back injury.
Discovered a puzzling problem with the DuckLight board. I noticed it was much brighter running off the 5v regulated supply of a USB port than it was off the 3xAAA battery pack. I thought this might be an amperage issue but a little more experimentation shows it to be voltage related.
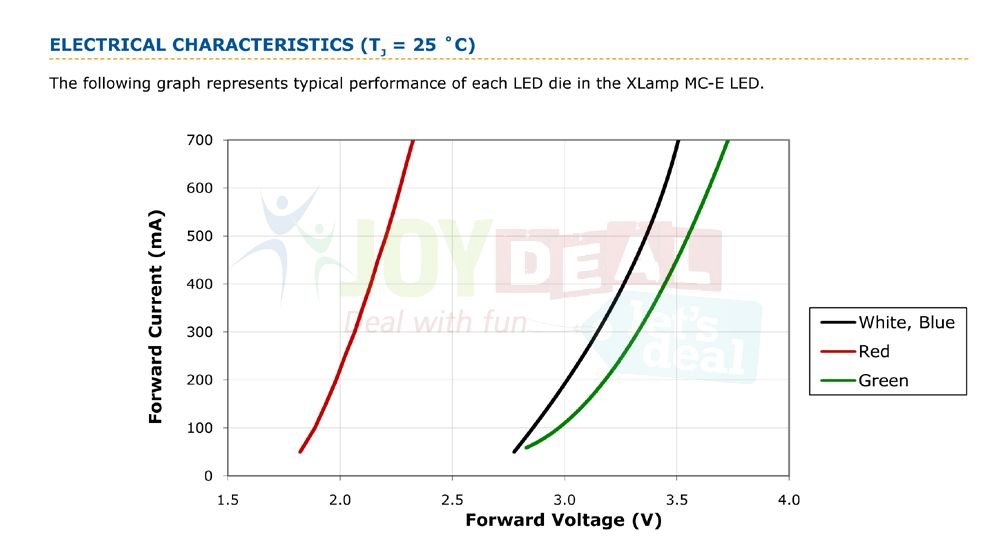
Oh, but wait. Calculating with the smaller voltage of nickel-metal hydride (the Sanyo Eneloop rechargeables I use almost exclusively) brings the 3x battery pack to a mere 3.6 volts. Which is far enough into the curve to experience a significant loss of luminosity.
And I had already discovered that on 2xAAA (my designed footprint for the first board) only the red LED lit properly; the green was obviously not getting sufficient voltage.
Well, shucks. The rated output on lithium polymer packs is 3.3 to 3.7 volts -- meaning once again that the most common green LED chemistry won't light at full power. Especially not if I try to run a 3.3 volt bus (to allow direct connection of certain sensors and XBee radios).
So what are the options? Switching to alkaline is not actually a help. Alkalines drop very rapidly in voltage from full charge. In addition, their nominal rating is given in no-load -- unlike NiMH's, which give the nominal voltage rating under design load (due basically to lower internal resistance).
Going significantly over and regulating down to 5 volts would make sense for a more complex project. At a draw of 1 watt or more, though, that's a hefty regulator -- and a lot of heat from wasted wattage. A dual NiMH pack, for instance, regulated to 5 volts, would have to burn off over five WATTS. That's at the peak of what a TO-220 package can handle with a bolt-on external heat sink.
Splitting the difference, a 4x battery pack delivers 4.8 volts nominal -- that's pushing up to 1/4 of the wattage into the regulator, which has to burn it off -- and at full charge can get pretty close to 6 volts. Which fortunately is while out of spec still within the range of what the ATtiny can tolerate! It is also twice the footprint of the board in flat pack and basically annoys me as a form factor even in quad.
(And in case you are wondering, all those Cree flashlights get away with it because "white" LEDs have a lower voltage drop than the common green ones.)
And, bah -- four fully charged eneloops are sufficiently above the voltage spec that the ATtiny shuts down. Which means I would need to include an LDO in order to operate the green LED at full efficiency. Or....regulate just the ATtiny, perhaps at 3.3V for sensor and XBee compatibility...well, according to the literature the AMC7135 really likes to be between 4.5v and 6v. Gets way too hot above that. Like most LDOs, the highest efficiency is when the voltage in is very close to the voltage out.
Well, I still have to finish porting my "blink" code to the new board, and see if there is even possibly enough space left over in program memory to do any of the other tricks I want. One issue from the old Piranha board that the Cree makes a lot more of a problem is the stair-stepping at the low end of the intensity scale. With only 255 steps in my pulse generator, the difference between 1/255 and 2/255 is a little too obvious in LED intensity. So I'm reading up on dithering techniques. (I can't simply increase the PWM bit depth, as I'm running at 8 MHz on internal oscillator and the PWM frequency is already close to critically low).
I also need to do a bake test to make sure the system can handle being ran wide open for a significant interval. I've already noted that 3W is at the low end of theatrical viability. Fortunately, a lot of applications can be served without full RBG -- instead hanging a 3W or even 10W single-color LED on the board and running the current regulators in parallel mode.
Another change that's on the horizon. The old RGBs are slipping in the Chinese suppliers to make room for new cheaper RGBW's. So far no affordable RGBA, but I have my eye on a few affordable RGB-Warm White already. Which is why my board is a four-channel. And why the ATtiny84 -- to give enough extra I/O pins for external sensors/controls. Although I still may end up just going into an ATmega eventually. Especially if I chose one with native USB support. Those are nasty little surface-mount jobbies...but at least they aren't BGA!
I'm also seriously contemplating revamping my headers completely and making the duckNode Trinket compatible. There's a LiPo backpack in that format, for instance. And in the obverse, I could make my XBee shield cross-compatible. The downside is I want to achieve everything possible from the ICSP header alone -- plus a stand-off, which the current iteration omits -- so there is no need to solder header pins to the board in order to program it or even to integrate it with radio link or power regulation. Having pins soldered on is one more thing to work around or to have to remove when cramming the final board into a prop, and the whole purpose of this exercise is to produce the most minimal footprint, lowest parts count and cost to bring full PWM control of 4W RGB/RGBW LEDs.
(So many TLAs there, I'm starting to feel like I work at NASA!)
Saturday, February 21, 2015
Dead Head
Ran out to the Rose Garden to take some pictures, but the roses are very much not in bloom at the moment. Whoops. We stayed until it got cold and dark anyhow. Yes; a sheet of foam-core works very well at providing a nice diffuse fill light....when there's enough direct light falling on it.
Ran the prototype current-controlled DuckLight for about four hours without any sign of overheating or the LED being overdriven. Next I think is an acid test; put a minimal heatsink on the LED and run it full-out for an hour or two. Those AMC7135's are totally the ticket!
The Holocron enquiry got one response. I'm working up a new Holocron design for a Jedi Academy now. Have in mind a combination I think will work, but haven't actually gotten into Illustrator (rather, InkScape) yet.
HP is now on my "nice" list. The scanner software I was using demanded I upgrade, told me upgrades were no longer free, and threw up its hands when presented with a 64-bit OS and what was apparently a 32-bit scanner driver. "Go call HP and see if they have any drivers," was all the software could offer. So I did, and HP had...a completely free and compatible scanner package I'm using now instead.
And I finally got off one sketch of the "art gun" direction for the raygun commission that I actually like.
Sure, I have to work on the proportions some more, and I have no idea how to machine some of it, but it in my mind finally achieves that blend of looking like the shape came out of art school but the details and machining are tight and quality.
It may not be quite period-looking enough, though. (Especially since to my mind the perfect combination would be stained and varnished wood furniture, and aluminium parts anodized in a pale green.)
So continue the sketches. Eventually I'll stumble upon a few that are decent enough to show to the client.
Ran the prototype current-controlled DuckLight for about four hours without any sign of overheating or the LED being overdriven. Next I think is an acid test; put a minimal heatsink on the LED and run it full-out for an hour or two. Those AMC7135's are totally the ticket!
The Holocron enquiry got one response. I'm working up a new Holocron design for a Jedi Academy now. Have in mind a combination I think will work, but haven't actually gotten into Illustrator (rather, InkScape) yet.
HP is now on my "nice" list. The scanner software I was using demanded I upgrade, told me upgrades were no longer free, and threw up its hands when presented with a 64-bit OS and what was apparently a 32-bit scanner driver. "Go call HP and see if they have any drivers," was all the software could offer. So I did, and HP had...a completely free and compatible scanner package I'm using now instead.
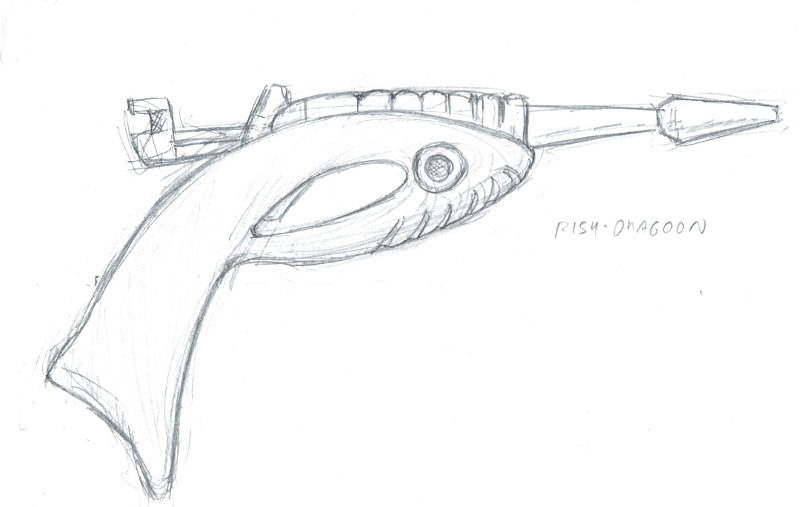
Sure, I have to work on the proportions some more, and I have no idea how to machine some of it, but it in my mind finally achieves that blend of looking like the shape came out of art school but the details and machining are tight and quality.
It may not be quite period-looking enough, though. (Especially since to my mind the perfect combination would be stained and varnished wood furniture, and aluminium parts anodized in a pale green.)
So continue the sketches. Eventually I'll stumble upon a few that are decent enough to show to the client.
Nile Project
Started the school tour (9 AM performances!) That show is open now, so another plate is quietly spinning...
Also shipped the next eight M40 grenades. That makes 35 of the things I've sold now. The new
processes didn't work quite as well as I wanted, and I still need to purchase some new tooling, but it got down to under three hours of labor each -- less than two for the machining.
Someone asked for the files on the Holocron and I've gone ahead and indicated I will produce a kit if requested. Perhaps I should start an INT thread at the RPF as well?
That makes the prop priority the Raygun. Although the final ship deadline is a ways off, it would be better business if I got it done a lot sooner -- soon enough for other "space tiki" fanatics to decide they want one, too.
And the AMC7135's I've been waiting on finally showed up. I enquired at a couple local stores for solder paste and checked prices at some online suppliers, but I was able to solder up the first SMD with a regular iron and some nice Kester silver solder I picked up at Al Lasher's Electronics.
There's a few mistakes on the PCB. I expected that. The trimpot sits too close to the ICSP header, and I'd managed to mis-identify the correct external clock pin for programming. Well, that's what jumpers are for.
The main purpose of the board was, after all, to test the AMC7135's. And after I fixed my screw-up with the ICSP wiring, it came through. I had to stop the full-power test because the LED needs a heat-sink if it is to be operated all out, but the AMC7135's appear to be limiting the current quite nicely, AND are responding correctly to the ATtiny. After a couple of hitches I have software PWM running. Seems a wee bit unstable -- so when I make the next version it will have a filter cap across the power lines of the DIP, and perhaps something on the RESET pin as well.
But before I get deep into revamping the PCB, I have software to write.
Also shipped the next eight M40 grenades. That makes 35 of the things I've sold now. The new
processes didn't work quite as well as I wanted, and I still need to purchase some new tooling, but it got down to under three hours of labor each -- less than two for the machining.
Someone asked for the files on the Holocron and I've gone ahead and indicated I will produce a kit if requested. Perhaps I should start an INT thread at the RPF as well?
That makes the prop priority the Raygun. Although the final ship deadline is a ways off, it would be better business if I got it done a lot sooner -- soon enough for other "space tiki" fanatics to decide they want one, too.
There's a few mistakes on the PCB. I expected that. The trimpot sits too close to the ICSP header, and I'd managed to mis-identify the correct external clock pin for programming. Well, that's what jumpers are for.
The main purpose of the board was, after all, to test the AMC7135's. And after I fixed my screw-up with the ICSP wiring, it came through. I had to stop the full-power test because the LED needs a heat-sink if it is to be operated all out, but the AMC7135's appear to be limiting the current quite nicely, AND are responding correctly to the ATtiny. After a couple of hitches I have software PWM running. Seems a wee bit unstable -- so when I make the next version it will have a filter cap across the power lines of the DIP, and perhaps something on the RESET pin as well.
But before I get deep into revamping the PCB, I have software to write.
Monday, February 16, 2015
Patch Pockets
Going into tech, no time or money for laundry. Needed to haul that sewing machine out to make more mic belts anyhow, so did some haphazard repairs on a couple pairs of torn pants. One had rear patch pockets. Which meant there was matching material I could salvage to cover a nasty hole.
Short two primers or my latest grenade order would be done. I hinted I'd make a ninth as a special gift to the customer by asking him to pick a number between M38 and M230. He picked M56, which doesn't help me at all -- is not one of the ones identified in the Aliens universe. Ah, well. Means I can do whichever one seems more interesting -- or least annoying.
Got up early and spent a long day repairing mic elements. Every time I dig into the bag full of broken elements, I find a couple more repairable ones trapped in the lining or under something else. I should be okay for the current show, then.
And the raygun got approved for metal. Metal, but still towards the Barbarella end. Which means is time to drop the whole "plywood cutout" idea and see what I can do if I free myself to imagine any kind of intersection I can machine (or CNC) between aluminium, brass, and acrylics.
Short two primers or my latest grenade order would be done. I hinted I'd make a ninth as a special gift to the customer by asking him to pick a number between M38 and M230. He picked M56, which doesn't help me at all -- is not one of the ones identified in the Aliens universe. Ah, well. Means I can do whichever one seems more interesting -- or least annoying.
Got up early and spent a long day repairing mic elements. Every time I dig into the bag full of broken elements, I find a couple more repairable ones trapped in the lining or under something else. I should be okay for the current show, then.
And the raygun got approved for metal. Metal, but still towards the Barbarella end. Which means is time to drop the whole "plywood cutout" idea and see what I can do if I free myself to imagine any kind of intersection I can machine (or CNC) between aluminium, brass, and acrylics.
Up Periscope
The hamster is sick over at my ISP and my regular internet connection is gone. Paying Xfinity for a short burst of service every day, like a boomer surfacing once a day to pick up new radio instructions.
Was a bit sick myself there and fell behind in finishing the last prop order. Work table is covered right now with M40 grenades getting the final going-over with emery paper and steel wool. Plus wireless microphone elements in need of repair before Tuesday tech rehearsal.
Saturday, February 14, 2015
Raygun VII
Put my Juan Garcia Esquivel CD up loud but the sketches are still not getting to where I want. Making step-wise progress in refining the various concepts, though.
ATG: Carved up my massing study; reduced the dimensions, made it taller, brought the handle inside the outline. It works better silhouette-wise, but the combination of rough wood/stone and the tech isn't working for me. I don't know if Tiki will abstract into harder, more mechanical lines, but it is worth a try. Maybe in a smaller clay maquette.
Art Gun: The acrylic fins aren't working for me. I'm not even sure how they attach anyhow. I have one more sketch to develop along that line, using narrow side fins at 45' angles. Acrylic disks would be easy to do and would light wonderfully, but I haven't been able to integrate them into a design. Also played around with milled slots or other cooling vents revealing a lit acrylic rod, but this feels like a more modern aesthetic.
Hair Dryer: On the simple side, could use some turned/machined elements. I'm still concerned about getting a good surface finish (as well as being strong and stable). A pull in ABS or tough acrylic would achieve gloss and color but that leaves edges and clean-up. Powder coating would be wonderful, but of course requires fabrication from metals. Very tin toy there, actually. Not that traditional paint is impossible -- but still fighting to go in a white or pink direction.
Tin Toy: possibly a big advantage to this is I think it is small. So holster-able, and easy to store, but also less metal or resin, faster CNC passes, etc. Of course less space inside for electronics, though. I have a strong suspicion this is going to be the leader, and I may need to back-burner the other ideas to push something of this up to where I can get a realistic budget on it. It seems likely it is going to be metallic -- cold-cast resin, metallic paints, or actual metal.
Perhaps at this point I need to take a different tack. The "tin toy" seems to be leading the pack as far as getting closest to what I think the client expects and leveraging the assets I have. But in any case a good question now is; what can I do within the low end of the budget projected?
Sunday, February 8, 2015
Raygun VI
Did a quick massing study of the ATG with scrap expanded polystyrene.
I need to rough out the components I mean to install, though. 2" speaker, and servo for the teeth. And two cree LEDs for the eyes (plus another backing up the mouth.)
I also think to get away further from the beer mug problem I might want to do some of that Alien Technology Has Hidden Lights look. Not quite sure what construction et al to make that happen, though.
(And, yes, first go-round at carving a Tiki head. It looks better than it photographs, but one thing I'm certain of is needs more horizontals. And the mouth, eye, and brow shapes need more to get across the ANGRY part of Angry Tiki God.)
Actually, if the trigger is "inside" the shell, can do a direct mechanical linkage to jaws and maybe eyebrows. Which would allow more expressive character. Basically a double-action; the slack of the trigger activates the jaws, and when it "clicks" it does the flashing light and sound effect.
I also feel I can integrate elements of the tiki head more with the user's hand. Place it higher and have it semi-visible across the top. Break up the "crown" more with air gaps. And I haven't ruled out doing a tiki body below the head -- but it would be extremely squat and stylized.
Also thinking again about the references the client linked to, which were very Tin Toy. More early 40's than mid-50's (and by 60's, remember, we're already into Star Trek.) This is plausibly yet another hybrid, with sculpted parts (rounded body, grip, some barrel elements) combined with some lathed elements (barrel rod).
There's a world of difference between a solid chunk of metal, and an assemblage of chrome and (illuminated) acrylic. And I need to nail this one down more before I get too far into planning. Fortunately I have five months until delivery!
So the "develop these designs far enough to turn in a proposal and sketch" list is up to four:
1) ATG. Which I'm going forward on anyhow as a project that amuses me. Looks like it is going to go in a Stargate SG-1 direction; dark stone with mysterious internal lighting, as if the Goa'uld had decided to go with Polynesian motif for their technology instead of Egyptian.
2) Hair Dryer. Single molded grip and body with rounded form and glossy surface -- possibly even pink. This is the one that pushes hardest towards animation, Duck Dodgers, squash and stretch, etc.
3) Art Gun. Acrylic and "chrome" (polished aluminium) with elaborate lighting system. Almost entirely machined. Since pistol is really not working with this, expand it to machine pistol lengths.
4) Tin Toy. Similar to the Hair Dryer in forms but more streamlined and serious, in harder-edged metallic treatments. Also incorporates some of the machined metal elements of the Art Gun.
Plasticity
I'm researching materials for my next prop build. Looking to see what in the way of tough, closed-cell foam, and lightweight carve-able foam can be run through the laser cutter. Finding out about turning acrylic on a metal lathe. Looking for suppliers for thermosetting plastic (TechShop doesn't have a lot at the front desk). Looking at existing shapes from Tap Plastics and other suppliers and doing quick calculations to see if any of the cheaper materials at Shapeways will fall within my project budget.
It continues to be a problem that TechShop is not a wide-open shop. Each group of tools requires check-out, and the check-outs cost money. Significant money -- the Water Jet SBU is over two hundred dollars.
Last time I was there, I ran off four M40 grenade bodies. Got it down to about 30-40 minutes each once I got into the swing of it, but my reservation ended, the shop was crowded, and I could feel myself starting to get careless. So time to step back from the whirring implement of doom and come back on Monday. So two more days should finish off my current order. And I have one more to add to my "scratch and dent" collection to put up at the RPF for the bargain hunters.
If I can work fast enough, I can design the armature for the ATG and run that off on the laser cutters during one of those trips next week. I think that one I will foam and glass it, but still contemplating CNC for the basic foam shapes. I wish I had ShopBot access already!
Ouch. I finally found PETG -- which is one of the three most-recommended materials for thermoforming -- at Grainger. I found pink insulation foam in handy 2' squares at Homely Despot -- Orchard seemingly carries it but their web store and search function are useless. Of course that foam can not be laser cut. Depron Foam, the absolute leader in a carve-able, laser cut-able foam, doesn't seem to be anywhere but a few chain hobby stores or online. So if I want to start bending metal...err...carving foam this week, it will have to be expanded polystyrene or one of the pricey carving foams (Balsa Foam) at the local Blick Art. At least OnlineMetals, my go-to for metal stock, has acrylic rod for a good price.
On reflection, easy-carving foam is a bad combination with thermoforming. The buck has to be able to withstand 14 psi plus the temperature of the heaters. So go with something that takes a little longer to carve -- MDF. Which can be laser-cut, so if I can figure out how to slice a model, I can do that to get a pretty good rough of the curves.
Tooling foam can also take the stresses, but I'm not sure what the local suppliers of that are. Or I could hand-cut 1" pink foam with my home scrollsaw, and cast the result in a silicone mold...
It continues to be a problem that TechShop is not a wide-open shop. Each group of tools requires check-out, and the check-outs cost money. Significant money -- the Water Jet SBU is over two hundred dollars.
Last time I was there, I ran off four M40 grenade bodies. Got it down to about 30-40 minutes each once I got into the swing of it, but my reservation ended, the shop was crowded, and I could feel myself starting to get careless. So time to step back from the whirring implement of doom and come back on Monday. So two more days should finish off my current order. And I have one more to add to my "scratch and dent" collection to put up at the RPF for the bargain hunters.
If I can work fast enough, I can design the armature for the ATG and run that off on the laser cutters during one of those trips next week. I think that one I will foam and glass it, but still contemplating CNC for the basic foam shapes. I wish I had ShopBot access already!
Ouch. I finally found PETG -- which is one of the three most-recommended materials for thermoforming -- at Grainger. I found pink insulation foam in handy 2' squares at Homely Despot -- Orchard seemingly carries it but their web store and search function are useless. Of course that foam can not be laser cut. Depron Foam, the absolute leader in a carve-able, laser cut-able foam, doesn't seem to be anywhere but a few chain hobby stores or online. So if I want to start bending metal...err...carving foam this week, it will have to be expanded polystyrene or one of the pricey carving foams (Balsa Foam) at the local Blick Art. At least OnlineMetals, my go-to for metal stock, has acrylic rod for a good price.
On reflection, easy-carving foam is a bad combination with thermoforming. The buck has to be able to withstand 14 psi plus the temperature of the heaters. So go with something that takes a little longer to carve -- MDF. Which can be laser-cut, so if I can figure out how to slice a model, I can do that to get a pretty good rough of the curves.
Tooling foam can also take the stresses, but I'm not sure what the local suppliers of that are. Or I could hand-cut 1" pink foam with my home scrollsaw, and cast the result in a silicone mold...
Saturday, February 7, 2015
Raygun V
Have a drawing for concept group #2 now. I just could not get the kind of boomerang-and-rod look I was after in a handgun. I think it requires a longer weapon, two-hand grip, with or without stock. For the shorter pistol lengths, acrylic furniture seems to work out better than MDF (although I haven't entirely ruled out aluminium sheet stock).
Design-wise, I miss the bounce and fun and exuberance of the other designs. And I also pretty much failed in capturing any of the Art School and Proud of It feeling of the Barbarella movie props.
The flat industrial look comes from the materials concept; the turned acrylic emitter is framed by symmetrical fingers in 1/4" acrylic, with the grip, trigger guard, and fin being extensions of these parts. It might be improved by moving to metal for the fingers, making the grip plates in CNC metal, and adding glossy red or black insulator rings between body and emitter.
But it is enough to move to trial analysis. The acrylic sheet parts are a quick laser job. The whole thing should be roughed out in CAD anyhow. The barrel rod is turned acrylic, which can be done on the metal lathe.
If there are internal electronics, then the rear cap should be practical. The drawing suggests it screws on -- hence the knurling -- but no reason it can't be magnets. I'm not eager to start threading on the lathe!
The grips are rounded and thickened with what is indicated as a black rubbery compound. Not sure what this is. Sugru would do but be expensive. Might be able to carve and sand urethane matts. Or perhaps print; the starburst is complex enough that it may make most sense as a 3d print, rather than trying to hand-carve a shape in clay then cast it.
I also haven't any solution yet for the trigger, which should probably be sprung and in any case is likely practical.
Because of the dimensions of some of the stock, and the need to print or mold some elements, materials cost is around a hundred even before adding electronics. CAD phase is 2-3 days, lathing a couple of days, assembly and clean-up finishes off into a second week.
I don't have a developed sketch for the "Hairdryer" (concept group #1) but there's enough to work on the essential problem. There's a good dozen methods I could use to form the sculpt (not counting hybrids and combinations). So far, though, I only have three strong ideas for making it sturdy enough for convention carry.
Slush-casting is the obvious one. But we're talking 60-100 bucks worth of silicone to cover that size of an object. Shell mold is possible, I suppose. In any case, this seriously pushes the budget.
Second alternative is to glass it. Resin-coat, then dig away the sculpt to provide some interior space. It isn't entirely destructive -- one could still make a casting off the finished piece. It also isn't as neat or as strong, and is a lot harder to work with in putting internal electronics in (I think!)
Third alternative is vacuum form. This might include a glassing stage just to make the master tough enough to take the 14 psi of the pulling process. And then the pull needs to be cleaned up and reinforced, as per my Instructable on the subject.
Out of all of them, glassing is the lead contender for coming in under budget. It is also, oddly, the most labor-intensive; because as time-consuming as cleaning up a pull is, doing all this work on the master is a lot tougher. I speak from experience.
Perhaps what needs to be folded into all of these, but this one in particular, is if I want to leverage economies of scale; intend from the start to make multiples and offer them in an Etsy store or something after the original order has had a chance to shine.
After working on it a bit more I think the best reinforcement also partial dictates construction. Cut two identical midline pieces from 1/8" MDF. Build up the shape in blue foam, tooling foam, or similar -- CNC'd if I can find a material well-suited to that. Carve, skin, sand traditionally. Then separate at the midline to create the two bucks for vacuum forming.
Oh, and Concept Group #3 faces the same class of problem. How to get a firm surface, made worse by the need to be thin and strong enough to support internal mechanism. I had originally thought of using a laser-cut acrylic framework that supports the sculpted elements, but that was before my research turned up that the basic shape is cylindrical, not square! But perhaps this is still plausible -- especially with CAD as a tool to plan the acrylic pieces...
One last interesting bit. I think this one really does want to be hand-carved. If there were more than one, each would have a unique personality.
The flat industrial look comes from the materials concept; the turned acrylic emitter is framed by symmetrical fingers in 1/4" acrylic, with the grip, trigger guard, and fin being extensions of these parts. It might be improved by moving to metal for the fingers, making the grip plates in CNC metal, and adding glossy red or black insulator rings between body and emitter.
But it is enough to move to trial analysis. The acrylic sheet parts are a quick laser job. The whole thing should be roughed out in CAD anyhow. The barrel rod is turned acrylic, which can be done on the metal lathe.
If there are internal electronics, then the rear cap should be practical. The drawing suggests it screws on -- hence the knurling -- but no reason it can't be magnets. I'm not eager to start threading on the lathe!
The grips are rounded and thickened with what is indicated as a black rubbery compound. Not sure what this is. Sugru would do but be expensive. Might be able to carve and sand urethane matts. Or perhaps print; the starburst is complex enough that it may make most sense as a 3d print, rather than trying to hand-carve a shape in clay then cast it.
I also haven't any solution yet for the trigger, which should probably be sprung and in any case is likely practical.
Because of the dimensions of some of the stock, and the need to print or mold some elements, materials cost is around a hundred even before adding electronics. CAD phase is 2-3 days, lathing a couple of days, assembly and clean-up finishes off into a second week.
I don't have a developed sketch for the "Hairdryer" (concept group #1) but there's enough to work on the essential problem. There's a good dozen methods I could use to form the sculpt (not counting hybrids and combinations). So far, though, I only have three strong ideas for making it sturdy enough for convention carry.
Slush-casting is the obvious one. But we're talking 60-100 bucks worth of silicone to cover that size of an object. Shell mold is possible, I suppose. In any case, this seriously pushes the budget.
Second alternative is to glass it. Resin-coat, then dig away the sculpt to provide some interior space. It isn't entirely destructive -- one could still make a casting off the finished piece. It also isn't as neat or as strong, and is a lot harder to work with in putting internal electronics in (I think!)
Third alternative is vacuum form. This might include a glassing stage just to make the master tough enough to take the 14 psi of the pulling process. And then the pull needs to be cleaned up and reinforced, as per my Instructable on the subject.
Out of all of them, glassing is the lead contender for coming in under budget. It is also, oddly, the most labor-intensive; because as time-consuming as cleaning up a pull is, doing all this work on the master is a lot tougher. I speak from experience.
Perhaps what needs to be folded into all of these, but this one in particular, is if I want to leverage economies of scale; intend from the start to make multiples and offer them in an Etsy store or something after the original order has had a chance to shine.
After working on it a bit more I think the best reinforcement also partial dictates construction. Cut two identical midline pieces from 1/8" MDF. Build up the shape in blue foam, tooling foam, or similar -- CNC'd if I can find a material well-suited to that. Carve, skin, sand traditionally. Then separate at the midline to create the two bucks for vacuum forming.
Oh, and Concept Group #3 faces the same class of problem. How to get a firm surface, made worse by the need to be thin and strong enough to support internal mechanism. I had originally thought of using a laser-cut acrylic framework that supports the sculpted elements, but that was before my research turned up that the basic shape is cylindrical, not square! But perhaps this is still plausible -- especially with CAD as a tool to plan the acrylic pieces...
One last interesting bit. I think this one really does want to be hand-carved. If there were more than one, each would have a unique personality.
Friday, February 6, 2015
Raygun IV
Emailed the client, and have additional notes and ideas. And a rough budget guideline, which on the surface of it removes a lot of processes from the list.
She does seem to be looking at silver metallic. I can certainly up-sell chrome, but candy pink may be a hard sell. Sigh. She also does seem to be open towards the kind of metal work that is, unfortunately, on the higher end for materials and time.
Still moving slowly, but tore off a bunch of quick sketches in trying to capture the concept of "flat shape holding turned shape." Aka something like plywood "stock" holding up a aluminium receiver and barrel. With swooped lines encompassing Streamline Moderne, Googie boomerangs, and Caddie fins, and some of the playfulness and Modern Art styling of the Barbarella movie props.
Towards the end there, I stumbled on some more streamlined and -- to my eye -- somewhat meaner looking shapes that use ribs/frames of laser-cut acrylic to frame narrower, simpler gun bodies/barrel tubes. These would also, of course, take lighting better.
Trouble with working with hard pencil lead, as I mentioned on my other journal; it doesn't scan well and it photographs even worse.
Previous to that I'd dashed off a couple of concepts of the "zepellin" gun -- a one-piece sculpted shape -- this time with the open "hair dryer" shape instead of the closed end of the previous sketches:
I think the one on the right really captures that Duck Dodgers playfulness -- you may notice the notation "Squash and stretch" next to it, aka, the deformations applied by animators to give life to their creations. But the sense I get from the material the client linked is of something slightly more serious.
I'm still going to do the Angry Tiki God gun, though. I've been looking at a lot of pictures of tiki heads in an attempt to internalize the language and motifs.
She does seem to be looking at silver metallic. I can certainly up-sell chrome, but candy pink may be a hard sell. Sigh. She also does seem to be open towards the kind of metal work that is, unfortunately, on the higher end for materials and time.
Still moving slowly, but tore off a bunch of quick sketches in trying to capture the concept of "flat shape holding turned shape." Aka something like plywood "stock" holding up a aluminium receiver and barrel. With swooped lines encompassing Streamline Moderne, Googie boomerangs, and Caddie fins, and some of the playfulness and Modern Art styling of the Barbarella movie props.
Towards the end there, I stumbled on some more streamlined and -- to my eye -- somewhat meaner looking shapes that use ribs/frames of laser-cut acrylic to frame narrower, simpler gun bodies/barrel tubes. These would also, of course, take lighting better.
Trouble with working with hard pencil lead, as I mentioned on my other journal; it doesn't scan well and it photographs even worse.
Previous to that I'd dashed off a couple of concepts of the "zepellin" gun -- a one-piece sculpted shape -- this time with the open "hair dryer" shape instead of the closed end of the previous sketches:
I think the one on the right really captures that Duck Dodgers playfulness -- you may notice the notation "Squash and stretch" next to it, aka, the deformations applied by animators to give life to their creations. But the sense I get from the material the client linked is of something slightly more serious.
I'm still going to do the Angry Tiki God gun, though. I've been looking at a lot of pictures of tiki heads in an attempt to internalize the language and motifs.
Thursday, February 5, 2015
Forms and Vacuums
Took the SBU at TechShop and have access to vacuum former now. Cute little machine; ceramic heaters, 24" bed, will pull up to 30 inches of mercury (aka a pretty good vacuum). They stock small amounts of PETG there, maybe a little ABS (and Tap Plastics is right down the road). So that puts new kinds of plastic shapes in range for the next prop.
Same day, I tried out new ideas for Aliens M40 grenade forming. The longer base cut still didn't clear the knurling tool, so back to the 16 degree angle for that. Installing the spring from the top does work, but I need a different drill bit to get a tighter fit on the hole. Although I was able to make the first one work with a little JB Weld. Since there's not enough time to make an order at McMaster-Carr, I'll assemble the current grenade order the same way as the previous ones.
I still haven't figured out a good way to make the button "click." The latest idea is to mill a narrow slot down the button and slip a piece of spring-steel wire in there. I also have no idea how to get the cap to pop off with that lovely sound. There isn't enough air space to create sufficient vacuum when it is thumbed off.
Annoyingly, the AMC7135's haven't arrived yet (and there is no tracking from that supplier). So I can't try out my PCBs.
And today seems to have been doldrums. Just haven't gotten a lot done in either design work or repairs.
Same day, I tried out new ideas for Aliens M40 grenade forming. The longer base cut still didn't clear the knurling tool, so back to the 16 degree angle for that. Installing the spring from the top does work, but I need a different drill bit to get a tighter fit on the hole. Although I was able to make the first one work with a little JB Weld. Since there's not enough time to make an order at McMaster-Carr, I'll assemble the current grenade order the same way as the previous ones.
I still haven't figured out a good way to make the button "click." The latest idea is to mill a narrow slot down the button and slip a piece of spring-steel wire in there. I also have no idea how to get the cap to pop off with that lovely sound. There isn't enough air space to create sufficient vacuum when it is thumbed off.
Annoyingly, the AMC7135's haven't arrived yet (and there is no tracking from that supplier). So I can't try out my PCBs.
And today seems to have been doldrums. Just haven't gotten a lot done in either design work or repairs.
Raygun III
Sorry for talking out the design process here. Usually I do it in a Scrivener document (makes a pretty handy framework for putting together index-card like threads of research and enquiry. The threading could be better, though).
Yes, I do go through this kind of process for everything I design. I'm not that smart. I have to work my way through instead of depending on that flash of inspiration.
But I believe in the importance of the design process. I've seen lots of lovely designs that are internally consistent and well executed but end up being inappropriate for the application. Or, at a step further removed, something like a set design which suits the play and the production and complements the costumes...but is too expensive for the company that's putting on the show.
It is very, very hard to recognize when you are putting boxes around your design process. When you allow yourself to be misled into taking an assumption or accident of process into an established framework for further design.
Thus, brainstorming, white-boarding, free-forming. Spending only enough time developing any specific idea to see where it will lead, then documenting it enough to pick up that thread later if needed before moving on to something different.
It also helps a lot to sleep on them. To let ideas sit for a little, then come back with fresh eyes. All in all, the most important (and sometimes the longest) part of the design process is the one from which the least visible outward progress is seen.
It also means one of the necessary skills is meta meta analysis; to realize when you've reached the point of diminishing returns (or your Gannt is showing the worst stack of dependencies reaches much too close to the deliverable date), and it is time to stop planning and start bending metal.
(Oh, yeah, and none of this thinking is original. In fact, there's a whole language of design out there that I wish I knew more of.)
My sleep-on it insights of today is that this design wants to be original. Not in concept or look, but in form; not shapes that are already out there, whether in full-blown form or in the form of toys or housewares that can easily be modified. This is for a family member, and she should be able to point at it as a unique creation. So once again I am led to fabrication or sculpting as the primary core.
This also means de-emphasizing reproducibility as a desired goal of the fabrication processes. Probably not going to be designed around molding, for instance.
Related to that, I want to show off. So fine surface finish. But also, some impetus towards getting effects that either do not seem possible or really are not possible with cardboard and poster paint.
Fold in one more aspect. I want to do what is fun. Fun includes both getting to use developed skills and trying out new techniques. But I also am paying for TechShop access, and there are several good reasons to want to show off what is possible with the kinds of tools that makes available. If nothing else, opening the eyes of potential future clients beyond the expectations of plywood-and-rattle-can construction.
(Not that there is anything wrong with plywood -- rather, MDF -- and rattle cans! They can and do get results a lot more professional than an outsider might expect.)
Also in the background, I have spent a fair amount of time developing the electronics knowledge and infrastructure to do interesting lighting and animation effects. And, as usual, there's techniques and ideas I've been meaning to try out some time; this project could be an excuse. As I said last post, this is also a good project in that I can let the needs of the electronics dictate more of the outward form than I might be able to in other kinds of props.
Balance all of this against what I can afford -- and what she can afford -- in terms of material and time. So a typical multi-variable problem. But I think it is now parameterized enough so I can move on to developing specific ideas to the point where they can be tested against the above requirements.
I've got three concepts now that are ready to move into trial development:
1) Zeppelin. After a little back-and-forth, currently conceived as a mono-body sculptural piece with fins and nozzle to be added. I have a number of possible methods to sculpt a body -- including something I'd love to try, which is thin foam CAD sliced -- but not sure of the approach to get a strong and stable shell of reasonable weight. It also is only suited for relatively primitive electronics.
The "hair dryer" form is basically similar as far as design and construction process. Incidentally, here's the list of words I jotted down as I was making the latest series of sketches: pink, chrome, starburst, cadillac fins, cheese holes, boomerang, bulbous, squash and stretch, streamline moderne, radar dish, engine bell, playful.
2) Barbarella. I haven't made much progress on the shape, but it fuses two classes of forms; turned shapes and flat shapes. Conceived as a cut-out in wood that supports a turned aluminium/laser-cut acrylic cylinder. The aesthetic to be swoopy, exuberant 60's curves. This is the option that uses the most power tools, with the final surface being defined largely by material and the shapes guided at least somewhat by internal electronics.
3) Angry Tiki God. Basically, cross a tiki with the Space 1999 laser pistol. Even better if the mouth can be motorized. And this is just too damn much fun not to do! And I've been reading up on clearomizers to see if it is possible for it to smoke a little as well...
Each of these is rather different in construction methods, design process, and final aesthetics. So they should provide plenty of information and ideas back as I attempt to develop them further.
Yes, I do go through this kind of process for everything I design. I'm not that smart. I have to work my way through instead of depending on that flash of inspiration.
But I believe in the importance of the design process. I've seen lots of lovely designs that are internally consistent and well executed but end up being inappropriate for the application. Or, at a step further removed, something like a set design which suits the play and the production and complements the costumes...but is too expensive for the company that's putting on the show.
It is very, very hard to recognize when you are putting boxes around your design process. When you allow yourself to be misled into taking an assumption or accident of process into an established framework for further design.
Thus, brainstorming, white-boarding, free-forming. Spending only enough time developing any specific idea to see where it will lead, then documenting it enough to pick up that thread later if needed before moving on to something different.
It also helps a lot to sleep on them. To let ideas sit for a little, then come back with fresh eyes. All in all, the most important (and sometimes the longest) part of the design process is the one from which the least visible outward progress is seen.
It also means one of the necessary skills is meta meta analysis; to realize when you've reached the point of diminishing returns (or your Gannt is showing the worst stack of dependencies reaches much too close to the deliverable date), and it is time to stop planning and start bending metal.
(Oh, yeah, and none of this thinking is original. In fact, there's a whole language of design out there that I wish I knew more of.)
My sleep-on it insights of today is that this design wants to be original. Not in concept or look, but in form; not shapes that are already out there, whether in full-blown form or in the form of toys or housewares that can easily be modified. This is for a family member, and she should be able to point at it as a unique creation. So once again I am led to fabrication or sculpting as the primary core.
This also means de-emphasizing reproducibility as a desired goal of the fabrication processes. Probably not going to be designed around molding, for instance.
Related to that, I want to show off. So fine surface finish. But also, some impetus towards getting effects that either do not seem possible or really are not possible with cardboard and poster paint.
Fold in one more aspect. I want to do what is fun. Fun includes both getting to use developed skills and trying out new techniques. But I also am paying for TechShop access, and there are several good reasons to want to show off what is possible with the kinds of tools that makes available. If nothing else, opening the eyes of potential future clients beyond the expectations of plywood-and-rattle-can construction.
(Not that there is anything wrong with plywood -- rather, MDF -- and rattle cans! They can and do get results a lot more professional than an outsider might expect.)
Also in the background, I have spent a fair amount of time developing the electronics knowledge and infrastructure to do interesting lighting and animation effects. And, as usual, there's techniques and ideas I've been meaning to try out some time; this project could be an excuse. As I said last post, this is also a good project in that I can let the needs of the electronics dictate more of the outward form than I might be able to in other kinds of props.
Balance all of this against what I can afford -- and what she can afford -- in terms of material and time. So a typical multi-variable problem. But I think it is now parameterized enough so I can move on to developing specific ideas to the point where they can be tested against the above requirements.
I've got three concepts now that are ready to move into trial development:
1) Zeppelin. After a little back-and-forth, currently conceived as a mono-body sculptural piece with fins and nozzle to be added. I have a number of possible methods to sculpt a body -- including something I'd love to try, which is thin foam CAD sliced -- but not sure of the approach to get a strong and stable shell of reasonable weight. It also is only suited for relatively primitive electronics.
The "hair dryer" form is basically similar as far as design and construction process. Incidentally, here's the list of words I jotted down as I was making the latest series of sketches: pink, chrome, starburst, cadillac fins, cheese holes, boomerang, bulbous, squash and stretch, streamline moderne, radar dish, engine bell, playful.
2) Barbarella. I haven't made much progress on the shape, but it fuses two classes of forms; turned shapes and flat shapes. Conceived as a cut-out in wood that supports a turned aluminium/laser-cut acrylic cylinder. The aesthetic to be swoopy, exuberant 60's curves. This is the option that uses the most power tools, with the final surface being defined largely by material and the shapes guided at least somewhat by internal electronics.
3) Angry Tiki God. Basically, cross a tiki with the Space 1999 laser pistol. Even better if the mouth can be motorized. And this is just too damn much fun not to do! And I've been reading up on clearomizers to see if it is possible for it to smoke a little as well...
Each of these is rather different in construction methods, design process, and final aesthetics. So they should provide plenty of information and ideas back as I attempt to develop them further.
Wednesday, February 4, 2015
Raygun II
Checked out local Dollar Stores (and a few other places) for plausible found objects I could use. As I am currently constructing it, there are sort of four classes of approach, more-or-less from easy to hard.
1) NERF repaints and existing model/resin kits. Only the latter has potential; the look we are after doesn't match much in the way of modern toys or props. I have a resin "Dex" gun from Sky Captain but it isn't a great pull -- cleaning it up to my standards is roughly equivalent labor to making my own from scratch. I may drop it in a paint bucket during this project just so I have something.
2) Found objects. Doesn't currently look plausible. Trouble is, you don't get platonic solids these days in consumer objects, whether hardware or household goods or plastic packaging. Everything is designed, with lots of little details. Details that are too obviously from the design sensibilities of this era. On the surface it sounds easy to glue a football onto the grips of a water pistol, but in practice there's way too much modification necessary to allow those parts to fit smoothly and look right when done.
Found objects works for Steampunk, but even then there is a fine line between a clever re-purposing of existing hardware, and the original hardware being a little too obvious.
This leaves me, for this project, essentially on the next two levels:
3) Traditional modeling. Building up with clay, foam, balsa, MDF, or some of the newer time-saving approaches like shopbot-carved MDF laminates or pepakura base. This can be one-off, or include molding stages to reduce weight and fragility, or be designed around the making of molds. The disadvantage in the latter is that molding material has a certain cost per volume and that puts some pretty firm lower limits on your project budget.
4) Full fabrication. I am making this term up as a catch-all phrase for working generally in industrial materials and with industrial processes; in metals, with milling, also with injection molding, powder coating, and other techniques that are not part of the traditional craft set. Obviously there's quite a bit of overlap, from laser-cutting acrylic to brazing brass, with the latter.
The methods and materials imply a greater cost, but for a project like this there is a trade-off; whereas if I traditionally model, I work from concept outwards to realization, focusing on fabrication means letting the materials and methods largely dictate design. So the elements of the final product are chosen because they fit well with selected fabrication techniques, and the final look is defined as much by the materials themselves as by various finishing processes (painting, decals, whatever).
Simultaneous with above, I'm working on general conceptions. One way or another I am going to do massing studies and mock-ups before I move to actual construction. It may or may not entail a stage of CAD modeling; for visualization, for client communication, to work out tolerances and fit-up questions, and potentially to drive various sorts of CNC fabrication.
At some point the two threads will meet in at least one plan that I can stick an estimate to and mail back.
I've only started scribbling design conceptions:
The major difference between the two larger sketches is one is "zeppelin on a pistol grip" and the other is "electric drill" -- aka, the body and grip are one solid object with no strong separation. The pig is the only idea I got from the Dollar Store. I haven't bothered to scribble out any of the stacks-of-rings or stacks-of-donuts or other typical barrel designs, but in my mind the barrel will be from 1/3 to 2/5 of the visual volume of the finished prop.
There are at least two more major forms I haven't been able to scribble out yet. One is what I might generically call the "slab of plywood with a dowel" look. This is also a mono-body, but with a smoothly tapering grip and a swoop to the overall shape that brings in the Cadillac Fin sort of idea.
"Hairdryer" is also a plausible direction, different from the "zeppelin" mostly in that there is no separate barrel but the muzzle opens out of the main body.
And yes, I really want Googie elements in this, boomerangs and cheese holes and all.
The other scribbles on that example above are just too modern and utilitarian and do not represent useful directions for this project (as much as I tried to work in Barbarella and Moonraker laser pistol elements into them.)
From even these, however, it appears obvious that however much I construct barrel elements from simple cylinders or lathed objects, the grip at least needs to be shaped more, and the body is an open question. So the likely plan is going to involve several different construction methods for the different elements.
1) NERF repaints and existing model/resin kits. Only the latter has potential; the look we are after doesn't match much in the way of modern toys or props. I have a resin "Dex" gun from Sky Captain but it isn't a great pull -- cleaning it up to my standards is roughly equivalent labor to making my own from scratch. I may drop it in a paint bucket during this project just so I have something.
2) Found objects. Doesn't currently look plausible. Trouble is, you don't get platonic solids these days in consumer objects, whether hardware or household goods or plastic packaging. Everything is designed, with lots of little details. Details that are too obviously from the design sensibilities of this era. On the surface it sounds easy to glue a football onto the grips of a water pistol, but in practice there's way too much modification necessary to allow those parts to fit smoothly and look right when done.
Found objects works for Steampunk, but even then there is a fine line between a clever re-purposing of existing hardware, and the original hardware being a little too obvious.
This leaves me, for this project, essentially on the next two levels:
3) Traditional modeling. Building up with clay, foam, balsa, MDF, or some of the newer time-saving approaches like shopbot-carved MDF laminates or pepakura base. This can be one-off, or include molding stages to reduce weight and fragility, or be designed around the making of molds. The disadvantage in the latter is that molding material has a certain cost per volume and that puts some pretty firm lower limits on your project budget.
4) Full fabrication. I am making this term up as a catch-all phrase for working generally in industrial materials and with industrial processes; in metals, with milling, also with injection molding, powder coating, and other techniques that are not part of the traditional craft set. Obviously there's quite a bit of overlap, from laser-cutting acrylic to brazing brass, with the latter.
The methods and materials imply a greater cost, but for a project like this there is a trade-off; whereas if I traditionally model, I work from concept outwards to realization, focusing on fabrication means letting the materials and methods largely dictate design. So the elements of the final product are chosen because they fit well with selected fabrication techniques, and the final look is defined as much by the materials themselves as by various finishing processes (painting, decals, whatever).
Simultaneous with above, I'm working on general conceptions. One way or another I am going to do massing studies and mock-ups before I move to actual construction. It may or may not entail a stage of CAD modeling; for visualization, for client communication, to work out tolerances and fit-up questions, and potentially to drive various sorts of CNC fabrication.
At some point the two threads will meet in at least one plan that I can stick an estimate to and mail back.
I've only started scribbling design conceptions:
The major difference between the two larger sketches is one is "zeppelin on a pistol grip" and the other is "electric drill" -- aka, the body and grip are one solid object with no strong separation. The pig is the only idea I got from the Dollar Store. I haven't bothered to scribble out any of the stacks-of-rings or stacks-of-donuts or other typical barrel designs, but in my mind the barrel will be from 1/3 to 2/5 of the visual volume of the finished prop.
There are at least two more major forms I haven't been able to scribble out yet. One is what I might generically call the "slab of plywood with a dowel" look. This is also a mono-body, but with a smoothly tapering grip and a swoop to the overall shape that brings in the Cadillac Fin sort of idea.
"Hairdryer" is also a plausible direction, different from the "zeppelin" mostly in that there is no separate barrel but the muzzle opens out of the main body.
And yes, I really want Googie elements in this, boomerangs and cheese holes and all.
The other scribbles on that example above are just too modern and utilitarian and do not represent useful directions for this project (as much as I tried to work in Barbarella and Moonraker laser pistol elements into them.)
From even these, however, it appears obvious that however much I construct barrel elements from simple cylinders or lathed objects, the grip at least needs to be shaped more, and the body is an open question. So the likely plan is going to involve several different construction methods for the different elements.
Tuesday, February 3, 2015
Raygun
I have a new commish. Still parameterizing it, though.
The original spec was "raygun." Which covers a lot of ground; in gross styles alone you have the "guns are bricks" modern gaming style, the increasingly iPhone look of recent movies, Steampunk, Atom Punk, Diesel Punk, punk punk, full-on Raygun Gothic (with or without Zeerust)...
And then there's question of cost/effort, which contains implicit aesthetic choices as well; budget prop making, high-end fabrication, resin kits, found-object construction (the classic mode of Steampunk prop building)...
And the quirkier subtleties of style within certain styles; for instance, the props from old serials (and the first of the Star Wars films) were very obviously mash-ups of easily available current weapons with bits of slapped-on fabrication. The ultimate expression of this being of course the Pulse Rifle from Aliens, which is a coherent designed object but reveals the Vietnam-era inspiration with every bit of carrying handle and Spas-12 cage left exposed.
Well, the second, more detailed spec is 50's-60's, leaning towards television and animation apparently, flashy shiny and even silly. Barbarella and The Jetsons specifically named. And the venue is a Tiki event, with the theme of early atomic age.
So that seems to point at classic animation/illustration design, the zepellin-bodied shapes with fins in chrome and bright-colored plastic.
And widening the brevet to include context, it needs to be sturdy enough (and not have too many fiddly bits sticking out) that it can survive a four-day convention. And it is good for it to be in bright colors and shapes that are far from modern handguns, because it will be in a public place.
And I can probably rule out trying to go in a tin toy or period prop shop aesthetic; my strong feeling is the aesthetic of the construction methods and finish is no more and no less than "shiny silly prop gun made with modern methods."
So, really, it is narrowing down to two tangentially related axis of design choice.
One being a rather amorphous Venn Diagram between Duck Dodgers, things that would not look out of place in a well-funded movie with retro aesthetics, and things that are defiantly artsy -- like some of the more fabulous props from Barbarella, such as the rifle whose stock was a silver-painted woman's hand.
The other axis is more or less cost, going from one-off constructions in found object and balsa carving to styrene and casting to metalwork.
Except that these two meet along a strange diagonal axis, that being a sort of materials-and-methods approach. Because when you are constructing something that isn't an exact replica you have a lot more freedom to let the material (or the construction method) determine the shape, indeed, the design and appearance.
Specifically, I can lathe, mill, and CNC aluminium, and I can take it up to a chrome-like polish. I can also easily lase complex shapes out of acrylic. On the other end of this axis, I could probably find basic shapes at the Dollar Store and slap an overall coat of shiny paint on them.
I've been thinking for quite a while about the lighting (and other effects) in props, and this is one of those cases where the mechanism can define the outer shape. Where form follows function, instead of trying to cram LEDs into a too-small space. One idea that came immediately when I started to think about this prop was the "cooling fin" look in acrylic rings, spaced carefully to be edge-lit from individual elements in a Neopixel stick -- meaning animated lighting effects are possible.
And at one more step of meta-design, this is an opportunity to explore fabrication techniques, design techniques, and materials. And it is a chance at exposure. So once again, even though an l'egg with a styrene fin painted in hot pink might be just as suitable -- even perhaps more suitable -- I am extremely tempted towards a largely aluminium-and-acrylic Barbarella-inspired art object designed implicitly around some fairly fancy-looking lighting effects.
Well. Perhaps the thing to do is...do both!
(I also can't help thinking of the period aesthetic in holsters, and that there is a vacuum-form class slot this week...)
The original spec was "raygun." Which covers a lot of ground; in gross styles alone you have the "guns are bricks" modern gaming style, the increasingly iPhone look of recent movies, Steampunk, Atom Punk, Diesel Punk, punk punk, full-on Raygun Gothic (with or without Zeerust)...
And then there's question of cost/effort, which contains implicit aesthetic choices as well; budget prop making, high-end fabrication, resin kits, found-object construction (the classic mode of Steampunk prop building)...
And the quirkier subtleties of style within certain styles; for instance, the props from old serials (and the first of the Star Wars films) were very obviously mash-ups of easily available current weapons with bits of slapped-on fabrication. The ultimate expression of this being of course the Pulse Rifle from Aliens, which is a coherent designed object but reveals the Vietnam-era inspiration with every bit of carrying handle and Spas-12 cage left exposed.
Well, the second, more detailed spec is 50's-60's, leaning towards television and animation apparently, flashy shiny and even silly. Barbarella and The Jetsons specifically named. And the venue is a Tiki event, with the theme of early atomic age.
So that seems to point at classic animation/illustration design, the zepellin-bodied shapes with fins in chrome and bright-colored plastic.
And widening the brevet to include context, it needs to be sturdy enough (and not have too many fiddly bits sticking out) that it can survive a four-day convention. And it is good for it to be in bright colors and shapes that are far from modern handguns, because it will be in a public place.
And I can probably rule out trying to go in a tin toy or period prop shop aesthetic; my strong feeling is the aesthetic of the construction methods and finish is no more and no less than "shiny silly prop gun made with modern methods."
So, really, it is narrowing down to two tangentially related axis of design choice.
One being a rather amorphous Venn Diagram between Duck Dodgers, things that would not look out of place in a well-funded movie with retro aesthetics, and things that are defiantly artsy -- like some of the more fabulous props from Barbarella, such as the rifle whose stock was a silver-painted woman's hand.
The other axis is more or less cost, going from one-off constructions in found object and balsa carving to styrene and casting to metalwork.
Except that these two meet along a strange diagonal axis, that being a sort of materials-and-methods approach. Because when you are constructing something that isn't an exact replica you have a lot more freedom to let the material (or the construction method) determine the shape, indeed, the design and appearance.
Specifically, I can lathe, mill, and CNC aluminium, and I can take it up to a chrome-like polish. I can also easily lase complex shapes out of acrylic. On the other end of this axis, I could probably find basic shapes at the Dollar Store and slap an overall coat of shiny paint on them.
I've been thinking for quite a while about the lighting (and other effects) in props, and this is one of those cases where the mechanism can define the outer shape. Where form follows function, instead of trying to cram LEDs into a too-small space. One idea that came immediately when I started to think about this prop was the "cooling fin" look in acrylic rings, spaced carefully to be edge-lit from individual elements in a Neopixel stick -- meaning animated lighting effects are possible.
And at one more step of meta-design, this is an opportunity to explore fabrication techniques, design techniques, and materials. And it is a chance at exposure. So once again, even though an l'egg with a styrene fin painted in hot pink might be just as suitable -- even perhaps more suitable -- I am extremely tempted towards a largely aluminium-and-acrylic Barbarella-inspired art object designed implicitly around some fairly fancy-looking lighting effects.
Well. Perhaps the thing to do is...do both!
(I also can't help thinking of the period aesthetic in holsters, and that there is a vacuum-form class slot this week...)
Begosh
The first PCBs arrived from OSH Park:
I partially populated one (nothing's soldered yet) to check if the footprints I designed in Eagle matched the parts I ordered from Digikey. So far, so good. Except that the key part -- the current limiters -- are coming via "International Airmail" from Fasttech and there is no tracking available.
Assuming the AMC7135's work -- which is really what this board is intended to test -- I already have a few ideas towards the next iteration. Probably drop the breadboard spacing for the outer pins, go to a lower profile trim pot and switch to SMT for the LEDs as well (so I can add more blinkenlights -- serial data, the traditional "pin 13 LED" of Arduino compatibles, and of course keep the power light.)
And I haven't quite figured out the best format for the XBee backpack (plus I keep searching for more budget-conscious alternatives to the XBee).
Here's what the board replaces:
That's the quick-and-dirty vero board version I made for the radio light. Only two channels on this one, as I was mixing red and green LED for a sort of amber light. That toggle you see is hot-glued to the side of a AAA battery pack. At least this iteration had the ICSP header, making it a little less annoying to tweak the software.
It was sitting inside this prop:
(Dress rehearsal photograph made by Anna Kaminska for Actor's Ensemble). Also taken before I replaced the ailing previous circuit with one that could reliably generate a decent amber.
So, sure, the new circuit is smaller, and as fast as I am with the vero board (or, rather, the somewhat expensive but totally worth it "Perma-Proto" stripboard from Adafruit) having already wired and partially programmed versions should make it a lot easier to add it to productions.
But more than that -- with wiring and programming already in place and basic options available just by turning a knob and hitting a button, this should be useable by people who don't have the time and experience to learn all this stuff themselves.
I partially populated one (nothing's soldered yet) to check if the footprints I designed in Eagle matched the parts I ordered from Digikey. So far, so good. Except that the key part -- the current limiters -- are coming via "International Airmail" from Fasttech and there is no tracking available.
Assuming the AMC7135's work -- which is really what this board is intended to test -- I already have a few ideas towards the next iteration. Probably drop the breadboard spacing for the outer pins, go to a lower profile trim pot and switch to SMT for the LEDs as well (so I can add more blinkenlights -- serial data, the traditional "pin 13 LED" of Arduino compatibles, and of course keep the power light.)
And I haven't quite figured out the best format for the XBee backpack (plus I keep searching for more budget-conscious alternatives to the XBee).
Here's what the board replaces:
That's the quick-and-dirty vero board version I made for the radio light. Only two channels on this one, as I was mixing red and green LED for a sort of amber light. That toggle you see is hot-glued to the side of a AAA battery pack. At least this iteration had the ICSP header, making it a little less annoying to tweak the software.
It was sitting inside this prop:
(Dress rehearsal photograph made by Anna Kaminska for Actor's Ensemble). Also taken before I replaced the ailing previous circuit with one that could reliably generate a decent amber.
So, sure, the new circuit is smaller, and as fast as I am with the vero board (or, rather, the somewhat expensive but totally worth it "Perma-Proto" stripboard from Adafruit) having already wired and partially programmed versions should make it a lot easier to add it to productions.
But more than that -- with wiring and programming already in place and basic options available just by turning a knob and hitting a button, this should be useable by people who don't have the time and experience to learn all this stuff themselves.
Monday, February 2, 2015
Cue up the Khachaturian
John D. McDonald was the first person I noticed using the plate-spinning act as a metaphor for juggling all the responsibilities of life and career. Years later it came briefly into vogue as a way to describe multi-tasking (which I always consider a way to do multiple things poorly; aka it is only worthwhile if none of the tasks actually require full concentration. Sadly, the task list of most people who employ the technique fails to meet that qualification.)
Being a full-time independent contractor/designer is like the clown version of this. Every time you manage to finish with one plate and put it away, someone hands you another one. You never seem to be quite able to put all of them away, so every time a plate or two needs extra attention, you can't help but be aware of the increasing wobble of all the ones in the back.
And like John D. MacDonald's example, if one plate gets in serious trouble it cascades. You only have enough time and hands to tend ones that are spinning decently...not a stack of plates that are all starting to teeter as one job goes into extra hours and deadlines on four other jobs are getting critically close.
Actually, the past two weeks more plates have gone down than have gone up. Peter Pan is closed, the show across town is struck, the Suomi is built. I have a grenade order with up to 16 hours of machining to go that is down to about 14 days before shipping, I have rental microphones going out in about six days that are going to need two days of work cleaning them up and testing them first, and I have a show going into tech in about two weeks as well. Last night I completed most of the lighting restore for the show that struck, and today I hope to complete that, then finish off an order of stage marker lights since the last parts just arrived on Friday.
Which means I'm pretty much due to add a few new plates.
Being a full-time independent contractor/designer is like the clown version of this. Every time you manage to finish with one plate and put it away, someone hands you another one. You never seem to be quite able to put all of them away, so every time a plate or two needs extra attention, you can't help but be aware of the increasing wobble of all the ones in the back.
And like John D. MacDonald's example, if one plate gets in serious trouble it cascades. You only have enough time and hands to tend ones that are spinning decently...not a stack of plates that are all starting to teeter as one job goes into extra hours and deadlines on four other jobs are getting critically close.
Actually, the past two weeks more plates have gone down than have gone up. Peter Pan is closed, the show across town is struck, the Suomi is built. I have a grenade order with up to 16 hours of machining to go that is down to about 14 days before shipping, I have rental microphones going out in about six days that are going to need two days of work cleaning them up and testing them first, and I have a show going into tech in about two weeks as well. Last night I completed most of the lighting restore for the show that struck, and today I hope to complete that, then finish off an order of stage marker lights since the last parts just arrived on Friday.
Which means I'm pretty much due to add a few new plates.
Sunday, February 1, 2015
Primeval
Where to start? I'd say, with the comment made on a paleobiology blog; "...that British-made sci-fi sitcom."
The show ran for five seasons and spawned a half-dozen novelizations and original books as well as a short-lived Canadian-made spin-off. The elevator pitch was likely something like "Torchwood with dinosaurs" and at that shallow level it delivers; a photogenic cast with entertaining dynamics having exciting encounters with paleontologically-based monsters-of-the-week while through the seasons slow revelations of a larger plot evolve.
Immediate plus point in that the prehistoric creatures presented -- although weighted heavily towards large and fierce apex predators -- were interesting and even obscure. It took them a long time to introduce a spinosaurus, and many of the beasties are various therapods somewhere along the long and murky trail from synapsids to early mammals.
And another in that status quo is far from god. They killed off major cast members and changed the methods and even focus multiple times. They also changed the style of the show along the different seasons, although this was even more of a mixed blessing.
First the science stuff. They obviously did their research, but they openly admit that pretty much everything was scaled up significantly. Their models were largely adopted from "Travels with Dinosaurs" which already put sensationalism and haste over accuracy, and in several episodes they drop even that pretense of academic support; one of the wee beasties is apparently drawn from the flights of fancy of long-time kook (but excellent illustrator) Dave Peters.
That said, paleontologists are a contentious lot. I have only anecdote but (outside of little incidents like Tycho Brahe's nose) it certainly seems that they are the most likely of the sciences to have their heated discussions break into fist fights. Their discussions and conventions seem rather more rough-and-tumble than you'd expect from, say, theoretical physicists. So one can't fault anyone, but particularly not a one-hour entertainment television slot, from simplifying the complex, contradictory and contentious state of our ever-increasing knowledge into something more coherent.
Actually, though, this is one of the major problems I have with the show as a presentation of science. They are far too certain. Especially since soft tissues are poorly recorded and details like coloration (not to mention wattles, frills, fronds, hair, feathers, etc.) are quite extrapolated, I find it hard to believe that every creature encountered even in the dimmest light is going to be amenable to spot identification.
Even the Spielberg trio did better than this; people in those movies were constantly being surprised by the live creatures, and as well taking the opportunity to explain that there were numerous contending theories before this new observation. In "Primeval" they do one internet search (or just pull up the information from their own memories) and immediately they know the body plan, habitat, and basic behavior.
Of course, in the show, pretty much all the behavior is stereotyped and simplistic. I haven't even seen the show draw attention to the difference between an ambush predator and a pack hunter. I don't even know how to classify the typical behavior shown in the show, except as Hollywood predation; they don't even seem to get around to actually eating their kills half the time, and are easily distracted from an easy kill or even a fresh kill by an active but distant distraction. Unlike natural behavior, even a wounded prey at their very feet is apparently less attractive than one that is yelling and waving sticks at them and running away at high speed. Maybe the chase instinct was overdeveloped in prehistoric times?
They do sometimes mention the specifics of the environment a creature has evolved in, or the special adaptions -- one may climb well, another can't tolerate heat, etc. But this is quite shallow, and tends to show up in the show as a Special Weakness they can exploit at the nth hour. So each encounter becomes largely formulaic, right down to the "Snarl for a while then leap" behavior of everything from large herbivores to (marine!) tube worms.
The rest of science gets even shorter shrift, of course.
In the mythos and development, this is where the evolving nature of the show shines. The first episode revealed a cluster of lights appearing in the Forest of Dean, which on investigation was a temporary portal to the late Permian. Unfortunately a local gorgonopsid had also strolled through the portal in the other direction, and was feeding on the local Brits.
This rapidly set a framework where our reluctant hero paleontologist Cutter, a geeky lab assistant, a herpetologist from the local zoo, and an experienced tracker/hunter, became the scientific advisors to a small military force run in top secrecy from some ministry or other that had the right combination of resources and luck to be saddled with this. Their basic goal was to learn when an anomaly opened, and to track down any incursions (aka local wildlife wandering in from whatever era was on the other side of the anomaly).
They early on lampshaded this rather bizarre team and the way our civilian stars soon took over the show by pointing out that they seemed to be very, very good at the job. Interesting was also the conservationist approach of Cutter, who whenever possible returned the animals to their own time. His attitudes seem to have infected the others, who rarely carried any weapon. (They preferred to MacGuyver their way around, but truth be said, their major approach to most problems seemed to be waving their arms shouting "Over here, ugly!" in turn, confusing the poor beastie until they could do something more effective.)
The mythos deepened when Cutter's wife was discovered still alive. In fact, very much alive and enjoying herself skinny-dipping in the Jurassic and stealing eggs for breakfast from pteranodons. Or whatever. She appeared to know a lot more than they did about where and when anomalies would appear, seemed to have the ability to move freely about time, and wanted Cutter to drop his work saving people from rampaging coleosaurs and join her sunning on a rock in the triassic instead.
And then came Season 2. Helen Cutter's interference caused a change in time, and Cutter came back to find the team now housed in the high-tech "ARC." Geeky Conner had gotten his first upgrade as well, now being a genius polymath who was able to quickly invent an anomaly detector. They all got haircuts, nicer jackets and more hair gel. And Helen got her own upgrade to, well, basically insane.
So core cast member Claudia vanished between seasons due to be edited out of history. Stephen bought it stopping one of those typical only-in-the-movies meglomaniacs who thought he could rule the world if he only had enough raptors with radio control collars (actually, Future Predators with fancy mind control things also from the future, but same idea). And Cutter got shot by Helen early into Season Three.
Egyptologist (and also mythology, language, cryptology, history and ethnology polymath) Sarah joins the cast straight from the Mummy Room at the British Museum, with strong hints that many of the creatures and stories from myth were the result of various anomalies, and some cultures may have understood and even exploited the things -- an intriguing new direction that lasted for all of one episode then was summarily dropped, with a brief encounter with a St. George like 14th-century knight the only sop to this potentially interesting angle.
Helen Cutter goes the rest of the way to madness and tries to single-handedly wipe out the Australopithicines (apparently Johansen didn't notice Lucy had been poisoned...) but is stopped at the climax of Season 3. And at least as of mid-season 4, all of her mysterious future technology, clone armies, and so forth died with her.
Season 4 brings on yet another batch of new characters, and gives our surviving starting roster of Connor and Abby even more buffs including a relationship upgrade. Sarah dies off-screen between seasons, and Danny only comes back briefly. And then the series veers off into yet another nutso industrialist trying to rule the world through Weird Science (although to his credit, he basically meant well).
All through this, the meat is still the monster of the week, but the format and feeling of these chases changes quite drastically, as does the overall flavor of the series. In general the earlier series are more serious, and the characters more grounded. Kudos again for not staying in status quo, but if they did my dream team would still be the original team, plus perhaps Sarah. Nuancing it, I'd take Cutter before his Season 2 haircut, Connor after his upgrade, Abby from her earlier cute phase but without the designated victim baggage of the first couple seasons. And more Rex.
But as for the show that never was... Well, the idea isn't bad. It is nice that someone thought about the implications of opening random doorways to another time, but it is a little sad that the major threat that wanders through happens to be the local apex predator more often than not. Population pyramids alone would suggest that for every Serengeti Lion, you'd see dozens of antelope first. Apex predators can't be the only creatures curious enough to go poking their head into the funny light!
And as visceral as two hundred pounds of snarling sabre-tooth meat is, the true risk of such passages would be such things as invasive species. Oddly enough this is never really mentioned. Although I do have to say it is harder to dramatize the existential threat posed by the Permian-incursion equivalent of rabbits being introduced to Australia.
The lack of any truly interesting or distinguishing behavior or other characteristics is also disheartening. There were exceptions. A few herd animals, some burrowers that were dangerous only by accident, a couple of parasites and even a fungus. And various aquatic beasties that had to be dealt with in mostly wetter ways.
As with all such gates through time and/or space, one has to wonder what would be the result if they weren't treated as one-off events kept hidden and access strictly controlled; if they were opened to market forces, with massed exploration, trade, tourism, exploitation of resources, and a whole host of entertaining problems resulting from that. That would be a very, very different show all right.
Another entertaining thought the series sort of addresses by default is that the toughest predator of the Cambrian is not necessarily tougher than a modern wide-mouthed bass. Now, evolution has no arrow. It is not intentional nor directional, and adaption is merely towards the optimum available trade-offs to the current environment.
That said, between us and the top of the food chain of a Permian ecosystem is 250 million years of tinkering around with new options in biology -- down to the molecular level, with better enzymes for muscle recovery, faster nervous conduction, etc. It would be easy to go too far with this -- and yes, humans are specialized largely in flexibility and plasticity, not in being Superman -- but I'd like to see someone play with the idea.
I mean, thanks to our extremely advanced thermal management system, not only can we remain active in very cold weather (large beasties get an advantage due to sheer bulk in this, so don't taunt the dinosaur caught in a snowstorm just on the basis of this) but on the right day we can run to the ground anything lacking sweat glands. Especially given that most predators emphasize the prey that is easy to catch over the prey that appears to be getting away, I'd think a lot of these encounters in any real biological and behavioral world would involve human sprinting like mad and early reptile breaking off pursuit after a short dash.
So I don't find it particularly astonishing that a well-adapted Terror Bird doesn't end up being fairly well matched against a human -- when said ornithoid is in unfamiliar (and cramped) human-built spaces and said human has the local equivalent of pointed stick. The lowly baseball bat or golf club may look a little ludicrous but it combines strength and a well-designed center of mass with a low enough weight to let it get up a pretty impressive swing.
The show ran for five seasons and spawned a half-dozen novelizations and original books as well as a short-lived Canadian-made spin-off. The elevator pitch was likely something like "Torchwood with dinosaurs" and at that shallow level it delivers; a photogenic cast with entertaining dynamics having exciting encounters with paleontologically-based monsters-of-the-week while through the seasons slow revelations of a larger plot evolve.
Immediate plus point in that the prehistoric creatures presented -- although weighted heavily towards large and fierce apex predators -- were interesting and even obscure. It took them a long time to introduce a spinosaurus, and many of the beasties are various therapods somewhere along the long and murky trail from synapsids to early mammals.
And another in that status quo is far from god. They killed off major cast members and changed the methods and even focus multiple times. They also changed the style of the show along the different seasons, although this was even more of a mixed blessing.
First the science stuff. They obviously did their research, but they openly admit that pretty much everything was scaled up significantly. Their models were largely adopted from "Travels with Dinosaurs" which already put sensationalism and haste over accuracy, and in several episodes they drop even that pretense of academic support; one of the wee beasties is apparently drawn from the flights of fancy of long-time kook (but excellent illustrator) Dave Peters.
That said, paleontologists are a contentious lot. I have only anecdote but (outside of little incidents like Tycho Brahe's nose) it certainly seems that they are the most likely of the sciences to have their heated discussions break into fist fights. Their discussions and conventions seem rather more rough-and-tumble than you'd expect from, say, theoretical physicists. So one can't fault anyone, but particularly not a one-hour entertainment television slot, from simplifying the complex, contradictory and contentious state of our ever-increasing knowledge into something more coherent.
Actually, though, this is one of the major problems I have with the show as a presentation of science. They are far too certain. Especially since soft tissues are poorly recorded and details like coloration (not to mention wattles, frills, fronds, hair, feathers, etc.) are quite extrapolated, I find it hard to believe that every creature encountered even in the dimmest light is going to be amenable to spot identification.
Even the Spielberg trio did better than this; people in those movies were constantly being surprised by the live creatures, and as well taking the opportunity to explain that there were numerous contending theories before this new observation. In "Primeval" they do one internet search (or just pull up the information from their own memories) and immediately they know the body plan, habitat, and basic behavior.
Of course, in the show, pretty much all the behavior is stereotyped and simplistic. I haven't even seen the show draw attention to the difference between an ambush predator and a pack hunter. I don't even know how to classify the typical behavior shown in the show, except as Hollywood predation; they don't even seem to get around to actually eating their kills half the time, and are easily distracted from an easy kill or even a fresh kill by an active but distant distraction. Unlike natural behavior, even a wounded prey at their very feet is apparently less attractive than one that is yelling and waving sticks at them and running away at high speed. Maybe the chase instinct was overdeveloped in prehistoric times?
They do sometimes mention the specifics of the environment a creature has evolved in, or the special adaptions -- one may climb well, another can't tolerate heat, etc. But this is quite shallow, and tends to show up in the show as a Special Weakness they can exploit at the nth hour. So each encounter becomes largely formulaic, right down to the "Snarl for a while then leap" behavior of everything from large herbivores to (marine!) tube worms.
The rest of science gets even shorter shrift, of course.
In the mythos and development, this is where the evolving nature of the show shines. The first episode revealed a cluster of lights appearing in the Forest of Dean, which on investigation was a temporary portal to the late Permian. Unfortunately a local gorgonopsid had also strolled through the portal in the other direction, and was feeding on the local Brits.
This rapidly set a framework where our reluctant hero paleontologist Cutter, a geeky lab assistant, a herpetologist from the local zoo, and an experienced tracker/hunter, became the scientific advisors to a small military force run in top secrecy from some ministry or other that had the right combination of resources and luck to be saddled with this. Their basic goal was to learn when an anomaly opened, and to track down any incursions (aka local wildlife wandering in from whatever era was on the other side of the anomaly).
They early on lampshaded this rather bizarre team and the way our civilian stars soon took over the show by pointing out that they seemed to be very, very good at the job. Interesting was also the conservationist approach of Cutter, who whenever possible returned the animals to their own time. His attitudes seem to have infected the others, who rarely carried any weapon. (They preferred to MacGuyver their way around, but truth be said, their major approach to most problems seemed to be waving their arms shouting "Over here, ugly!" in turn, confusing the poor beastie until they could do something more effective.)
The mythos deepened when Cutter's wife was discovered still alive. In fact, very much alive and enjoying herself skinny-dipping in the Jurassic and stealing eggs for breakfast from pteranodons. Or whatever. She appeared to know a lot more than they did about where and when anomalies would appear, seemed to have the ability to move freely about time, and wanted Cutter to drop his work saving people from rampaging coleosaurs and join her sunning on a rock in the triassic instead.
And then came Season 2. Helen Cutter's interference caused a change in time, and Cutter came back to find the team now housed in the high-tech "ARC." Geeky Conner had gotten his first upgrade as well, now being a genius polymath who was able to quickly invent an anomaly detector. They all got haircuts, nicer jackets and more hair gel. And Helen got her own upgrade to, well, basically insane.
So core cast member Claudia vanished between seasons due to be edited out of history. Stephen bought it stopping one of those typical only-in-the-movies meglomaniacs who thought he could rule the world if he only had enough raptors with radio control collars (actually, Future Predators with fancy mind control things also from the future, but same idea). And Cutter got shot by Helen early into Season Three.
Egyptologist (and also mythology, language, cryptology, history and ethnology polymath) Sarah joins the cast straight from the Mummy Room at the British Museum, with strong hints that many of the creatures and stories from myth were the result of various anomalies, and some cultures may have understood and even exploited the things -- an intriguing new direction that lasted for all of one episode then was summarily dropped, with a brief encounter with a St. George like 14th-century knight the only sop to this potentially interesting angle.
Helen Cutter goes the rest of the way to madness and tries to single-handedly wipe out the Australopithicines (apparently Johansen didn't notice Lucy had been poisoned...) but is stopped at the climax of Season 3. And at least as of mid-season 4, all of her mysterious future technology, clone armies, and so forth died with her.
Season 4 brings on yet another batch of new characters, and gives our surviving starting roster of Connor and Abby even more buffs including a relationship upgrade. Sarah dies off-screen between seasons, and Danny only comes back briefly. And then the series veers off into yet another nutso industrialist trying to rule the world through Weird Science (although to his credit, he basically meant well).
All through this, the meat is still the monster of the week, but the format and feeling of these chases changes quite drastically, as does the overall flavor of the series. In general the earlier series are more serious, and the characters more grounded. Kudos again for not staying in status quo, but if they did my dream team would still be the original team, plus perhaps Sarah. Nuancing it, I'd take Cutter before his Season 2 haircut, Connor after his upgrade, Abby from her earlier cute phase but without the designated victim baggage of the first couple seasons. And more Rex.
But as for the show that never was... Well, the idea isn't bad. It is nice that someone thought about the implications of opening random doorways to another time, but it is a little sad that the major threat that wanders through happens to be the local apex predator more often than not. Population pyramids alone would suggest that for every Serengeti Lion, you'd see dozens of antelope first. Apex predators can't be the only creatures curious enough to go poking their head into the funny light!
And as visceral as two hundred pounds of snarling sabre-tooth meat is, the true risk of such passages would be such things as invasive species. Oddly enough this is never really mentioned. Although I do have to say it is harder to dramatize the existential threat posed by the Permian-incursion equivalent of rabbits being introduced to Australia.
The lack of any truly interesting or distinguishing behavior or other characteristics is also disheartening. There were exceptions. A few herd animals, some burrowers that were dangerous only by accident, a couple of parasites and even a fungus. And various aquatic beasties that had to be dealt with in mostly wetter ways.
As with all such gates through time and/or space, one has to wonder what would be the result if they weren't treated as one-off events kept hidden and access strictly controlled; if they were opened to market forces, with massed exploration, trade, tourism, exploitation of resources, and a whole host of entertaining problems resulting from that. That would be a very, very different show all right.
Another entertaining thought the series sort of addresses by default is that the toughest predator of the Cambrian is not necessarily tougher than a modern wide-mouthed bass. Now, evolution has no arrow. It is not intentional nor directional, and adaption is merely towards the optimum available trade-offs to the current environment.
That said, between us and the top of the food chain of a Permian ecosystem is 250 million years of tinkering around with new options in biology -- down to the molecular level, with better enzymes for muscle recovery, faster nervous conduction, etc. It would be easy to go too far with this -- and yes, humans are specialized largely in flexibility and plasticity, not in being Superman -- but I'd like to see someone play with the idea.
I mean, thanks to our extremely advanced thermal management system, not only can we remain active in very cold weather (large beasties get an advantage due to sheer bulk in this, so don't taunt the dinosaur caught in a snowstorm just on the basis of this) but on the right day we can run to the ground anything lacking sweat glands. Especially given that most predators emphasize the prey that is easy to catch over the prey that appears to be getting away, I'd think a lot of these encounters in any real biological and behavioral world would involve human sprinting like mad and early reptile breaking off pursuit after a short dash.
So I don't find it particularly astonishing that a well-adapted Terror Bird doesn't end up being fairly well matched against a human -- when said ornithoid is in unfamiliar (and cramped) human-built spaces and said human has the local equivalent of pointed stick. The lowly baseball bat or golf club may look a little ludicrous but it combines strength and a well-designed center of mass with a low enough weight to let it get up a pretty impressive swing.
Subscribe to:
Posts (Atom)