Well, like the story of Basho and the Fish, getting to the point where you press that button is actually a lot of work. What these new tools are, is just another form of jig (or "tooling," if you want to use the fancy aerospace term).
I used a lot of jigs when I was a full-time theater carpenter (that is, a set builder). We'd spray-paint them red so they didn't get thrown out by accident. One show I had to make a whole bunch of fake bolt heads as decorations for some massive girders. Underside of a bridge or something; I don't remember now. Ripped down 1x to 2", cut it into 2" squares, cut off the corners to make a hex shape, then routed around the top. I spent most of a day making a complicated jig that would hold the thing in place for all the cuts and routes.
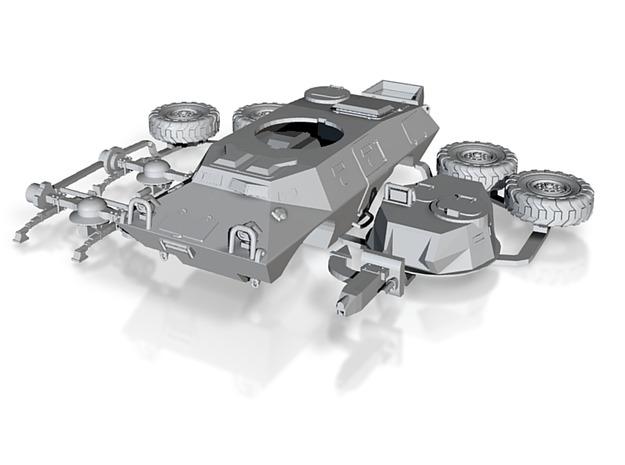
And, well, you'd think -- for all that computing power you have to throw behind the design process, it still takes horrendously long.
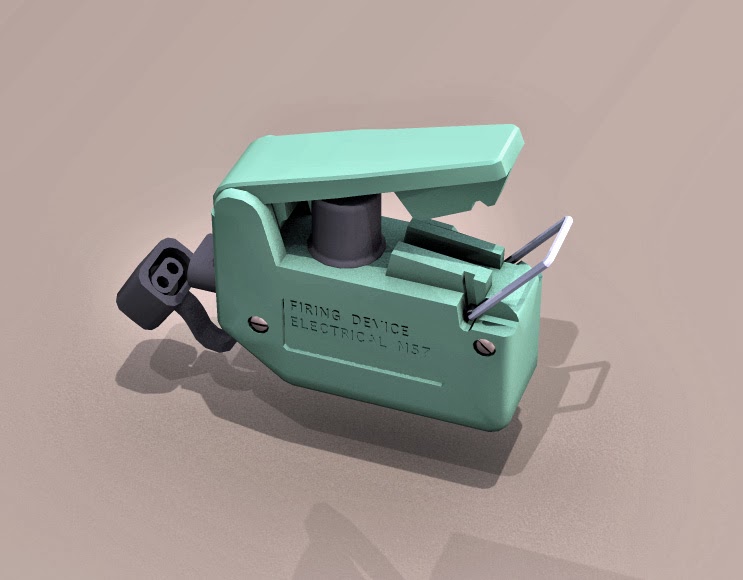
My old penlight finally died and I thought of yet another project that would be very cute. To wit; a penlight in the shape of a Sonic Screwdriver. But not any of the existing ones; a very small one built around a single AAA cell -- not the dual AA versions which won't fit in a pocket, or the ones using weird rare batteries that are a pain to replace. AAA, with a boost circuit driving half a watt of narrow-beam colored light (we almost always use colored light backstage. Tradition.)
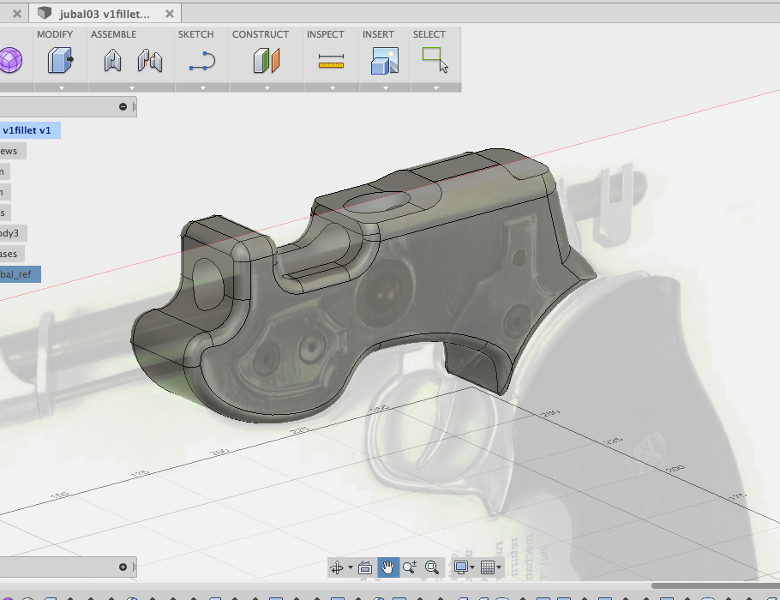
But that requires going into the CAD software and figuring out a casing that can be printed or machined that fits the available components and looks at least something like the sonic of choice (I'm partial to a War Doctor sonic, myself, which is basically a Tom Baker sonic with a different top).
Also back on one of those rear burners is the Jubal Early CNC model. And a turned flash hider for a "King of the Rocketmen" pistol.
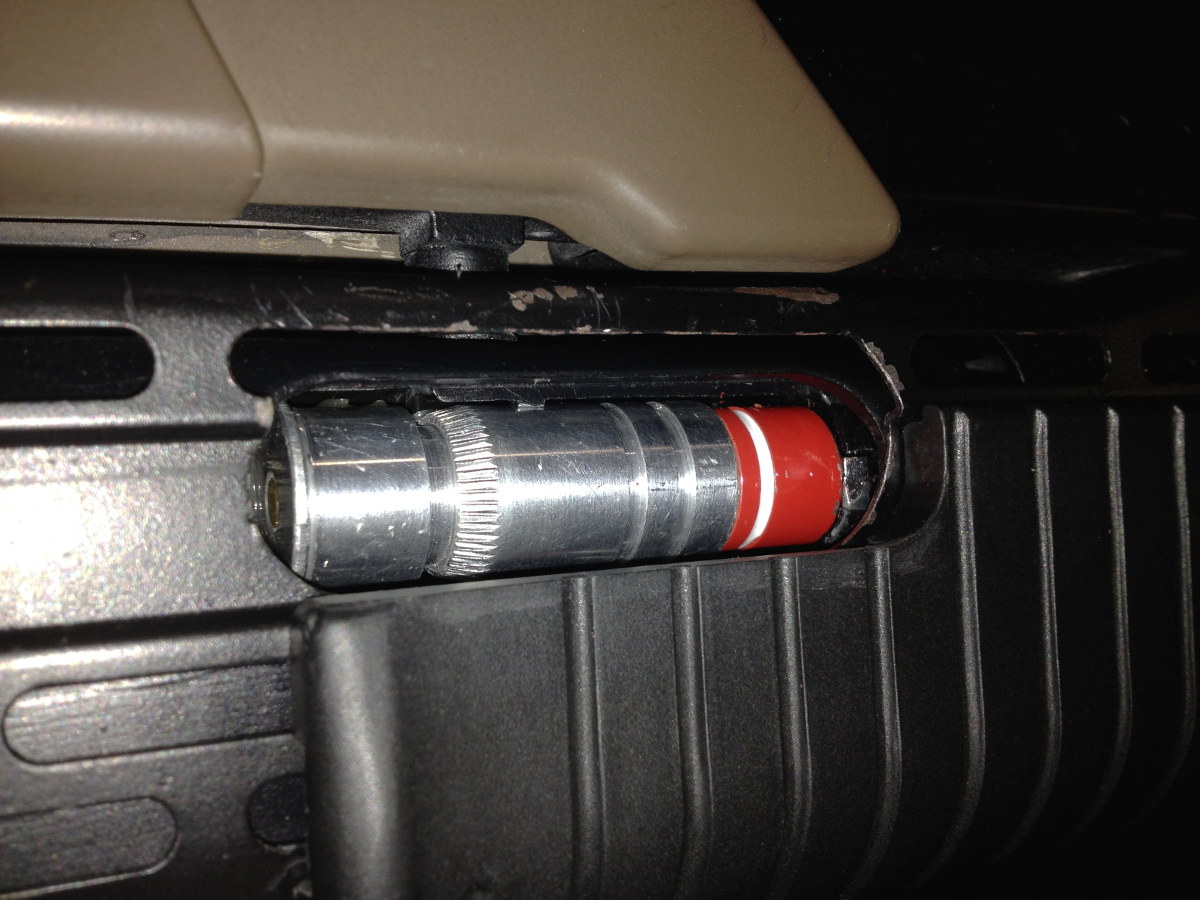
I've been really pushing on the DuckLight PCB -- working it up in Fritzing at the moment, which seems to be working and saves me the time of learning Eagle properly. Using the prototype in another show helped a lot. I'm getting excited about this thing and think it may be a very useful little trick for the prop-maker's arsenal.
I'm going with an ATtiny84 now. Four channels of software PWM current-controlled to 350ma means you can run a cheap RGB "Cree" LED, an RGBW, or a single-channel LED of up to three watts in bridging mode. ICSP header for the experienced programmer, software serial I/O...and there's enough I/O pins left on the '84 to put in a Program Select button. So the end-user can dial up a bunch of basic effects right on the board, without needing to connect up a computer. The XBee option will be on a daughterboard, though; there's just no space for the pin footprint.
I fully intend this to be offered in kit form. And at this point I've solved enough of the electronics and programming issues I really am ready to make up the first batch of PCB's.
No comments:
Post a Comment